電纜云母帶生產工藝揭秘,從礦物到高性能絕緣材料的蛻變之路
發布時間:2025-03-07 瀏覽:62次
導語
在電力傳輸與高端裝備制造領域,電纜云母帶憑借其耐高溫、抗電擊穿、化學穩定性強的特性,成為高壓電纜絕緣層的核心材料。然而,這種看似普通的帶狀材料背后,卻隱藏著一套融合礦物加工、精密復合與智能控制的復雜工藝體系。本文將帶您深入生產線,解密電纜云母帶從原料篩選到成品包裝的全流程技術細節。
一、原料選擇:天然云母與合成材料的博弈
電纜云母帶的核心原料是云母礦物,但并非所有云母都符合工業標準。生產商通常優先選擇白云母(Muscovite)或金云母(Phlogopite),這兩種礦物因介電強度高(可達150-200 kV/mm)、熱穩定性優異(耐受溫度達800℃以上)而備受青睞。
實際生產中,天然云母需經過破碎→水力分選→磁選除鐵三道預處理工序,將雜質含量控制在0.3%以下。隨著環保要求升級,部分企業開始采用合成云母紙,通過高溫熔融法制備的氟金云母,其厚度均勻性比天然云母提升40%,更適合自動化生產線。
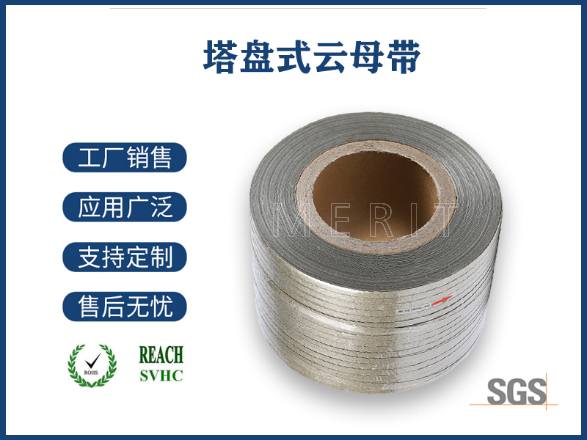
二、云母紙處理:微米級精度的技術突破
云母紙的制備直接決定最終產品的絕緣性能。主流工藝采用濕法抄造技術:
- 漿料配制:將云母碎片與去離子水按1:50比例混合,加入0.5%-1%的聚丙烯酰胺分散劑
- 纖維解離:通過高壓均質機使云母鱗片剝離至5-10μm厚度
- 抄造成型:在長網造紙機上形成定量30-80g/㎡的基材,干燥后含水率需嚴格控制在2.5%±0.3%
*關鍵創新點*在于梯度化結構設計:部分企業通過疊加2-3層不同粒徑的云母層(表層5μm、中層10μm、底層15μm),使擊穿電壓提升至35kV/mm以上,比傳統單層結構提高27%。
三、復合工藝:粘合劑與增強材料的協同效應
裸云母紙需通過復合工藝增強機械性能。生產線通常配備四輥逆涂布機,以0.05mm精度涂布特種粘合劑:
- 有機硅樹脂:耐溫等級達180℃,適合常規電纜
- 聚酰亞胺:耐溫300℃以上,用于核電、航空航天領域
- 磷酸鹽無機膠:完全不含有機物,滿足無鹵阻燃要求
*進階工藝*采用玻纖布/聚酯薄膜雙面增強:
- 在云母紙單面復合8μm厚聚酯薄膜,拉伸強度提升至120N/cm
- 另一面層壓40g/㎡的E型玻纖布,使縱向抗張強度達到200N/cm2
- 通過熱壓輥(180℃、0.5MPa壓力)實現三層材料的分子級結合
四、智能質控:六大關鍵參數實時監測
現代生產線配備在線檢測系統,通過以下指標確保產品一致性:
- 厚度公差:0.08±0.005mm(采用β射線測厚儀)
- 介損角正切值:50Hz下≤0.002(自動介電測試儀每10米抽檢)
- 透氣度:≤5mL/min(符合GB/T?5591.5-2018標準)
- 膠粘劑固化度:紅外光譜法檢測交聯度≥85%
- 抗張強度:縱向≥100N/cm,橫向≥80N/cm
- 云母覆蓋率:數字圖像分析系統確保≥98%
*典型案例*顯示,引入機器視覺檢測后,云母帶表面缺陷檢出率從人工檢測的92%提升至99.7%,每年可減少質量索賠損失超300萬元。
五、環保升級:廢料回收與能源優化
在雙碳目標驅動下,行業正推進三大綠色變革:
- 水循環系統:抄造工序用水量從10噸/噸產品降至3.5噸
- 余熱回用:干燥箱排氣熱量用于預熱新鮮空氣,節能率18%
- 邊角料再生:將分切廢料粉碎后重新制漿,原料利用率從89%提升至96%
某上市公司通過光伏+儲能改造,使生產線綜合電耗降低至1200kWh/噸,較行業平均水平下降22%,年減少碳排放量達4800噸。
通過上述流程可見,電纜云母帶的生產絕非簡單疊加材料,而是材料科學、精密機械、智能控制的多學科集成。隨著新能源汽車充電樁、特高壓電網等新興領域的需求爆發,這一傳統行業正通過技術創新,持續為電力傳輸安全保駕護航。
TAG: